Which Sewing Line System is Right for Your Production?
- The Purnaa Team
- Dec 22, 2020
- 5 min read
Updated: Jan 4, 2021
By Alex Berryman

An efficient sewing line is essential to any cut-and-sew business - it is a building block of efficiency and the quality of a product. But not all sewing lines are created equal nor are all types of lines appropriate for different production needs. Knowing their strengths and weaknesses can help you choose the manufacturer with the best practices for your needs.
Here we explore 3 common sewing line layouts used in the industry, then look at how Purnaa determines which layout to use, taking into consideration our clients' production requirements and also the goal of furthering Purnaa's social mission to employ survivors of exploitation and marginalized people.
Keywords:
Work stations - the individual machine where a worker will execute a number of operations
Operation - one step of the sewing process (ex. sewing the hem, joining the sleeve, etc).
Work in Progress - The number of products that have begun to be assembled, but have not been finished
Bundles - packs of works in progress
Skill Center/ Process Layout:
In all sewing lines, the product goes from station to station until they reach completion. But instead of being arranged in a sequence, a skill center or process layout arranges its workstations by function. Machines and personnel of similar functions will be organized into separate rooms - called skill centers - and bundles will pass to each skill center throughout the facility until the product is complete.

This system is known for its excellent line balancing and managing absenteeism. Depending on the facility's capacity, each skill center can be working on multiple bundles and products at once, allowing for many SKUs to be passed through the whole system at one time. Each machine technician is a specialist on the machines in their skill center. If a person is absent from work, those in that skill center can take on their work without disrupting the whole line.
That being said, managing a skill center facility is much like being an air traffic controller. With so many bundles and SKUs passing between each skill center, confusion between a production manager and lineworkers results in large delays for the customer.
Another issue is quality assurance. This is because skill centered layouts can have thousands of items in progress. Each bundle that passes between the skill center can have hundreds of units; if an error occurs, hundreds or thousands of units could be in process by the time the first bundle reaches QC. The production manager and QC team would then have to backtrack to identify where the issue occurred and rework all the units that have passed through that skill center. This can create huge delays in a project!
Product Line Layout:
A product line is more like what most people think of in garment manufacturing, with work stations assembled sequentially. This means each production line is designed around the product, which means it is great for long production runs and is often used by manufacturers that specialize in one product type.

A product line layout is advantageous because it is simply managed - often you can see a product be made, from start to finish, in one room. As a result, quality checks can happen while production is still underway, meaning an issue can be identified and rectified sooner, and less rework will have to be done.
The one key issue with a product line layout is maintaining a balanced line. Each workstation must take the same amount of time as the rest, or else bottlenecks occur - costing both time and money in production. When working with a manufacturer that uses a product line layout, you can ask them how they will design the line and what the operation time is for each workstation - this can indicate how efficiently your product is being made.
Additionally, the product line layout is heavily dependent on each individual worker at each station. An absent worker can upset the balance of the flow. Also, one slow worker can cause a bottleneck. This can lead to intense pressure on individual workers if not managed well.
Module system / Toyota system
A modular system or the Toyota system is similar to the product line layout except instead of one technician per work station, the workers can move up and down the production line, executing multiple operations on multiple workstations. This system is much more fluid and dynamic, naturally balancing the line. Additionally, it cuts down on the pieces in progress, having the same number of pieces in progress as those working the line. Worker flexibility to move up and down the line makes the system more robust to absenteeism than a line system. It also eliminates bottle-necks at steps that take more time because workers can pass their pieces on to the next worker and move back to a previous station.

A drawback is that this production process requires the highest skilled workers as each must be cross-trained on multiple machines. This can limit the employment pool and require more skilled, and therefore more expensive labor.
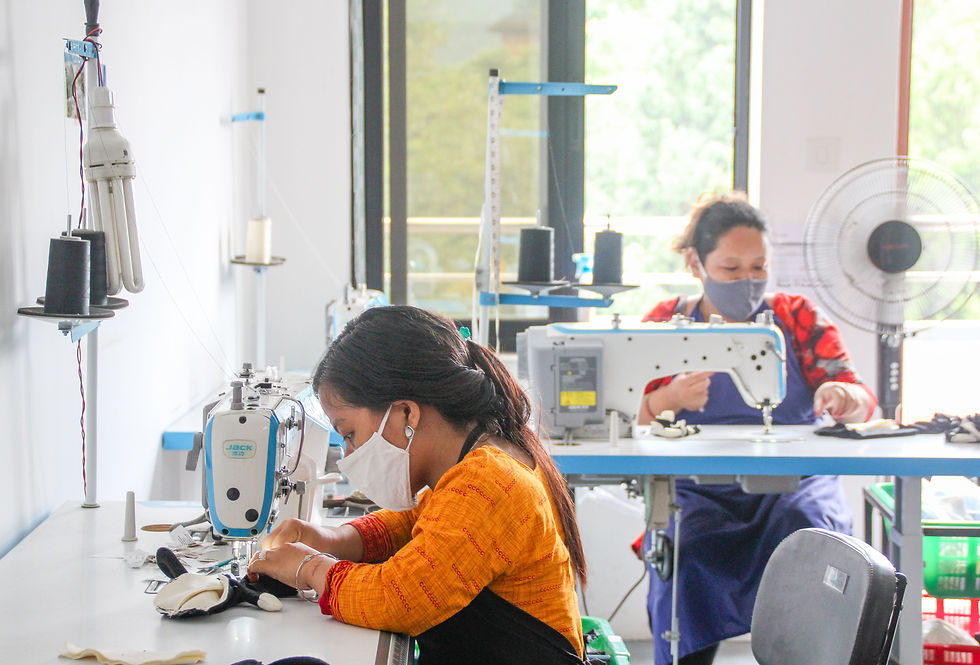
Purnaa's Method:
At Purnaa, while productivity and efficiency are important to us, we also look to create a dignified work environment for all Purnaa staff who often come from marginalized backgrounds. We use a Product Line system with additional supporting workers that enables many principles from the Toyota System, such as reducing work in process and immediate QC checks, but also accommodates staff that may not have the flexible skill required to move efficiently between production steps.
The How:
At Purnaa, we have the following teams that allow us to effectively produce our customer's products:
4 teams, composed of 7 sewers and 1 team leader
Set up team
Floater team
QC team
Our 4 teams are the core of our sewing operation, set up in a product line layout. Our setup team plans out and establishes the workstation sequence for each new production run; determining where each workstation is to be placed and what operations are to be done at each workstation. The team leader assigns each person to a workstation according to their strengths. Then the teams and production leadership train each worker to do their operations, adjusting as needed to ensure a balanced line. If a person is absent, a member of the "floater team" can come and take their position without disrupting the production line. Then at the end, we have a QC team that checks the products coming off the line and working with the sewing team to troubleshoot any issues that may arise.
Team Prerana, Team Laliguras, Team Danfe, Team Ekata respectivly.
The Why:
Our mission is to empower fresh starts and fulfilled lives through excellent jobs, and in doing so, we must evaluate how we equip and empower staff through their work. As a majority of our social impact is among our sewing staff, the sewing line layout is integral to our social impact.
We are committed to hiring at least 50% of our staff from marginalized backgrounds. In Nepal, marginalized people often have a history of physical and emotional trauma. Many grow up without the opportunity to attend school. This makes training new skills very difficult, and while we love to challenge staff to achieve their full potential, we do recognize that an ill-suited job is not empowering. As a result, we have tailored our training and production line accordingly.
At Purnaa, we believe that caring for people and making a quality product efficiently is not mutually exclusive. If you would like to start manufacturing with Purnaa submit your design here, or learn more about us by emailing us at info@purnaa.com
Comentarios